Using 5S Warehouse Checklists
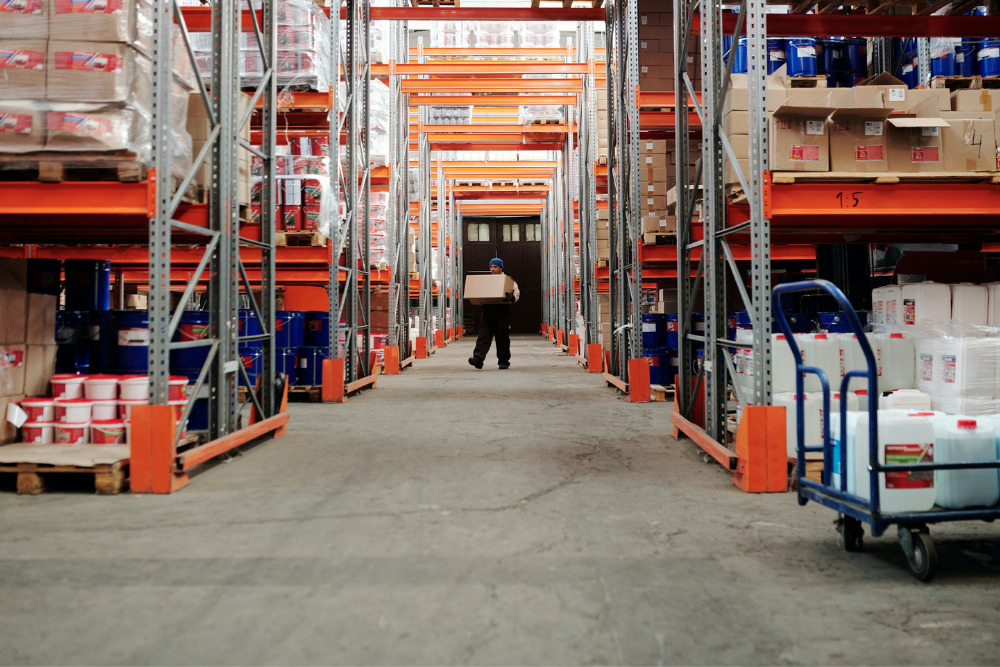
A warehouse can feel chaotic at the best of times. And it can spiral out of control when left unchecked. Safety decreases, accidents increase, and inventory is misplaced, mismanaged, and missing (intentionally or by mistake). A carefully managed warehouse is a safe and productive warehouse. One of the simplest things you can do towards that end is to keep everything clean, neat, and tidy. And you’ll find some of the best tools in 5S warehouse checklists.
Using 5S Warehouse Methodology
Originating in Japan, the 5S methodology is a straightforward system for keeping a workspace—office, warehouse, or otherwise—operating at optimum levels. If you’ve ever heard the expression “a place for everything, and everything in its place,” this functions on the same level.
The ideas behind 5S warehouse checklists are far from superficial. An organized and tidy workspace not only looks good, but it also increases productivity, efficiency, and safety. Properly implemented, the 5S system boosts everything that needs a boost and makes it quick and easy to identify and address issues before they become major headaches.
While no one is sure who created the 5S methodology, it rose to prominence at Toyota in the 1970s. In Japan, the 5S are seiri, seiton, seiso, seiketsu, and shitsuke. In an English setting, 5S warehouse checklists include:
- Sort
- Set in Order
- Shine
- Standardize
- Sustain
But what does each mean, and how can you apply them to warehouse management? Let’s find out.
The First S: Sort
Thanks to advocates like Marie Kondo, the minimalist trend has swept through every facet of life. If something doesn’t “spark joy,” as Kondo would say, get rid of it. (Kondo has since embraced the occasional mess as part of parenthood, but her influence continues.)
In a warehouse setting, “joy” is more aptly “necessity.” Disorganization in a warehouse is an accident waiting to happen, and employees waste time looking for things. Sort through inventory and assets, and discard whatever you no longer need.
- What items are in the warehouse but are not used there?
- What things clutter up the workspace and consume valuable space?
- When was the last time someone used a particular item?
- What can you remove, recycle, or replace?
Sort and discard. Revisit as necessary.
The Second S: Set in Order
Once sorted, it’s time to put everything in its place. This is likely the most demanding step in the warehouse 5S audit. Take the time to do it right, because it will impact the rest of the checklist.
Consider the workflow within the warehouse. Identify the assets and resources that the team uses most frequently and set these in prominent, logical locations.
- Which employees use this most and when?
- Can I move these to a better location?
- How can I simplify the overall organization of inventory?
- Are there any existing bottlenecks that you can eliminate?
- Can you further segment groups into sub-groups to make finding a specific item or resource faster?
Signs, floor and aisle markers, labels, and inventory tags can assist with this step.
Revisit as necessary.
The Third S: Shine
No one wants to work in a filthy space. There’s a reason people say “cleanliness is next to godliness.”
Give the warehouse a thorough cleaning, including floors, shelves, and surfaces. Dust, sweep, and mop. Or, in other words, shine.
Then, implement a shine schedule to keep everything sparkling. Identify things to be done daily, weekly, monthly, quarterly, and yearly. Clean up spills and leaks immediately, as they look bad and are a safety hazard. Purchase appropriate spill kits. Keep heavy machinery clean and maintained. Don’t forget about loading docks and break areas.
Hire janitors and cleaners if the budget allows for it. Employees can and should be responsible for keeping their personal workspace clean and tidy. Assign responsibilities to individuals on a rotating basis for shared spaces. Have supplies available and accessible to that end.
A clean warehouse creates an environment that employees are proud of and want to help succeed.
The Fourth S: Standardize
You’ve sorted, set, and shined. Now, consistency is key. It’s a waste of everyone’s time if you complete the first three steps, but then ignore and forget what you’ve established.
Create a warehouse “bible” that outlines the steps, procedures, and processes to keep everything in tip-top shape. Use straightforward language. Distribute copies to employees and have additional copies available in strategic spots throughout the warehouse.
Standardize how to deal with equipment breakdowns, various spills, and other emergencies. There should never be an incident without a clearly defined and existing response. Create checklists for starting a shift, ending a shift, end-of-day, and more.
Hang work posters and charts that outline workflows. Standardize onboarding new employees and ongoing training for existing staff.
Consistency is key.
The Fifth S: Sustain
Now, focus on consistency.
A sustained process becomes a habit, and a habit becomes a part of the company’s culture. The goal is to make the 5S mentality a natural part of the workday. If it happens without constant reminders, it’s well on its way.
A focus on cleanliness and organization makes a struggling warehouse better and a good warehouse great. Regular evaluation and inspection—both planned and surprise—are crucial steps at this stage.
- Is everything that needs to be done actually getting done?
- Is it completed to the best of everyone’s abilities?
- Are the new standards making it easier and safer or more difficult for employees? And if not, what can you adjust to change that?
- Is there a feedback channel in place for employees to share their thoughts?
Beyond these basics, there are plenty of other 5S warehouse checklists out there to make getting started and maintaining this practice a simple task. No excuses.
Introducing a Sixth S: Security
While the 5S warehouse operations checklist has been proving its value for decades, there is perhaps a sixth S to add to the system: security. And that’s where Deep Sentinel comes in.
Proper workplace security is pivotal to success in the modern world. You need to protect against threats from without and within. And a robust security solution that includes business security cameras is the best tool for the task.
Deep Sentinel’s warehouse security solutions are unrivaled in the industry. With Deep Sentinel, you’ll get the only warehouse security package that comes with guards—active monitoring by live guards—included. Cameras, AI, and LiveSentinel surveillance guards protect your warehouse against theft, vandalism, break-ins, loitering, and other unwanted guests. Every single day.
How does it work? Motion-activated HD cameras monitor your perimeter. Then, artificial intelligence categorizes all movement as either harmless—which the system dismisses—or a potential security risk. At this point, it instantly notifies live guards who assess, intervene, and engage with the suspect. If necessary, the guards notify police of a verified crime in progress, which elicits a prompt response.
So while the 5S methodology improves productivity and efficiency, adding Security as a sixth S improves protection, too. Protect your employees, protect against losses, and protect your profits.
Keep it neat, tidy, and secure. That’s the warehouse we all want to see. And it’s easier than you think with Deep Sentinel. Get your free consultation today.
Need a Solution that Prevents Crime?
Deep Sentinel is the only security technology that delivers the experience of a personal guard on every customer’s home and business. Visit deepsentinel.com/business or call 833-983-6006